The worldwide glass bottle making industry saw a revolution in operations during the first quarter of the 20th century. It is hard to overstate the importance of the first patented, fully-automated glass-blowing machine, known as the “Owens Machine,” within that revolution. That machine, with the ability to produce more bottles of more regular size and capacity, revolutionized the glass industry and forever changed related industries like the packaging, shipping, and beer industries. While a hand-blowing bottle glass house could only be expected to produce 3600 pint-sized bottles in a 24-hour period, the first Owens model (“A”) could produce 17,280 (Skrabec 2007:208). In addition, where one blower and at least two boys were needed on a mold to produce every bottle, two Owens machines with six molds each required three men (Glass Bottle Blowers’ Association 1912:37), eliminating the need for advanced bottle blowing skills and child labor while improving efficiency. Much has been written about the Owens machine and its impact on business, so only a short summary is included here (see Barnett 1925b; Meigh 1960; Cable 2005; Miller and McNichol 2012).
The Owens Bottle Machine Company (OBMCo) of Toledo, Ohio, applied for the patent on the Owens Machine (Google Patents 1904) in the United States on April 13, 1903. The patent was granted on August 2, 1904. The machine was the culmination of more than a decade of inventions, patents, and experimentation by glassmaker and factory superintendent Michael J. Owens and engineer Emil Bock (and others), along with encouragement and investment by glass industry millionaire Edward Drummond Libbey. The original patent and all later improvements placed the OBMCo at the forefront of a complete overhaul of the glass industry. There were many markets outside of the U.S. where the Owens machine could save labor costs and improve profits, and the OBMCo wasted no time in approaching those markets. As the efficacy of the machine was proven and improved upon, competition intensified worldwide for bottle makers to either license and install the machines in their factories or to invent their own machines.
Short Video Showing Seams
This was a short video I recorded to show how the Owens scar is really a parison mould scar and that it is what the side ghost seams are related to.
Ghost
Seams
Ghost seams are the remnants of the original parison mould that forms the size and general shape of the bottle before the parison is moved into the final mould and fully blown. The parison is cut by a metal "knife" to sheer off extra glass creating the Owen's scar with the feathering on or near the base of the bottle - the Owens scar is also a ghost seam as it is not part of the final mould's seams. The side ghost seams are not as obvious and are not usually straight, but are still from the parison mould.
Owens
Scars

A
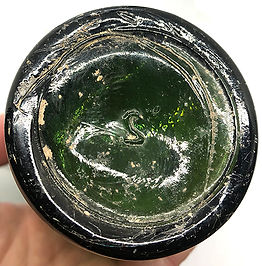
B


C
D
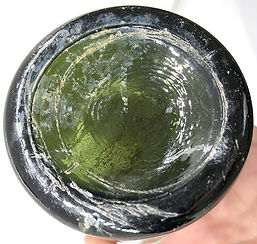
E
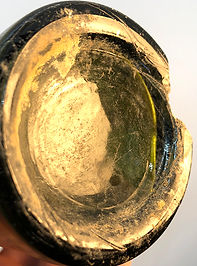
F

G
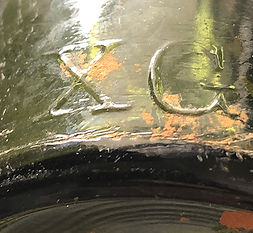
H
A - a small, tidy Owens scar with little feathering
B - a larger, untidy Owens scar with visible feathering
C - harder to see, but there is definite feathering at the top of the photo
D - in this case, the feathery Owens scar is visible and extends off the base to the heel on the left side of the photo
E - Feathering of Owens scar can be seen at bottom. Because of the mess on the bottom of this bottle, it is a little harder to differentiate the mold seams and scars
F - Owens scar is irregular but central. Final seam runs along the foot of the bottle
G - Owens scar is irregular but central. Little feathering.
H - Owens scar is runs up onto the heel of the bottle note feathering under the "XG" mark.
Side Ghost Seams
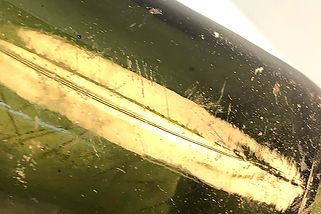