
Semi-Automatic Machine-made Bottles
The first Semi-Automatic Bottle Making Machines able to make small-mouthed and -necked vessels like beer bottles, were based on the premise that one person would put a gob of metal (liquid glass) into a machine, a second person would operate the machine (using pedals and levers), and a third would take a completed bottle out of the machine. The machine switched out parison and body moulds and blew air into the bottle. As time proceeded, more of the processes became automated, and fewer people were needed to make a bottle, but there was always a person involved. Fully automated machines, the first being the Owens Machine, were designed to operate without a person needing to participate, only to oversee the work.
​
In order for a person to load the metal (liquid glass) into the small finish mould of a semi-automatic machine, the parison mould had to be inverted with the base-end of the parison mould being open and facing upward. Every machine did this a little bit differently. Some left the top completely open and allowed gravity to help the glass flow into the finish mould. Others used pressure to push the glass into the finish mould - either with a plunger or with air. The parison would then be rotated to an upright position for the bottle to be blown.
The Boucher machine from France used compressed air to make sure the glass was pushed down and filled the finish mould. It was able to produce bases with an indent (necessary for wine bottles) with a second mould that the soft bottle was placed into. I suspect that many wine bottles produced between 1900-1914 in France were made in these machines, but I also think they might have been heat treated after being removed from the machine, so you will not see seams on them. More study and research will be necessary on this one.
Various patents show the Inverted parison and/or the upright body moulds.
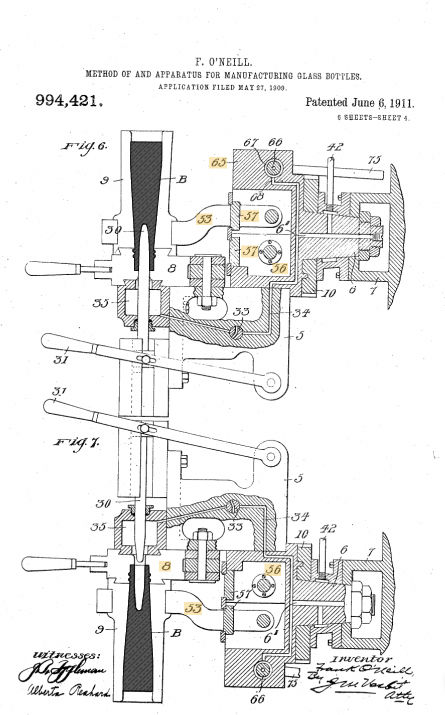



This clip is showing the side ghost seams of a semi-automatic machine-made bottle like the one before it, but doesn't have talking over it
These are 6 imperial ounce bottles made in a semi-automatic bottle making machine. The Ashley Machine was invented in England in 1887. It was the first semi-automatic machine that made output at the bottle factory much faster. Because of the size and colour, I believe this beer bottle was made in Europe. American beer bottles at the turn of the 20th century tended to be larger than 6 oz and were usually amber in colour (not always). You'll note that the parison mould seam goes about 1/3 of the way down the bottle (shown in photograph). The side mould seam runs parallel to it and runs from the base to the neck seam just under the finish to the post bottom seam on the bottom of the bottle. The finish has only one seam going up and over the finish. The crown closure was invented in 1892, so this bottle definitely post-dates that - probably a few years later due to the context in which it was found. The Owens fully-automated machine have ghost seams coming up from the bottom, these semi-automatics have irregular seams coming down from the finish.


This is the top of a Walker's Kilmarnock Whisky bottle. I believe it was made the Simpson Bradshaw semi-automatic bottle making machine developed by John Lumb. In the early part of the 20th century, Walker's (now Johnnie Walker's) decided that getting machine-made bottles would speed up and localize production. Later, they did not want to be beholden to the Owen's European Bottle Machine Company (Morgan 2020, Chapter 7, p.9). So they went with John Lumb and Co., who had designed their own machine, the Simpson Bradshaw. Note the mould seems going around the bottle below and above the string rim and the ghost seams going down the neck (you don't get ghost seams high up on the neck of an Owen's bottle). You can also just barely see a seam going up the lip (or finish) straight up from the side seam (right). Bottom left you can see the ghost seam, started in the photo above, continuing down on the neck and shoulder and in the bottom right fading out on the shoulder of the bottle.
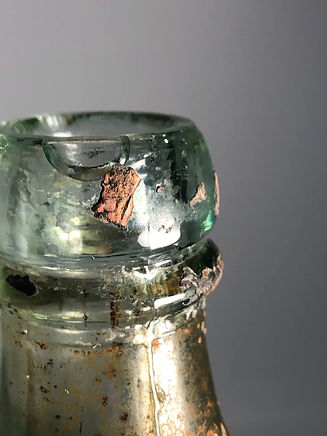


This partial bottle clearly shows the truncated ghost seam coming from the finish down. It is marked with a "C" on the base and a three digit code.

The Root Company of Terre Haut, Indiana had their own semi-automatic machine called the Red Devil. It was developed between 1905 and 1912. They did good business in beer bottles, but seem to have made their name in soda bottles.
The O'Neill semi-automatic machine was patented in 1911. Patent 994,421A, (https://sha.org/bottle/pdffiles/ONeillmachines.pdf)
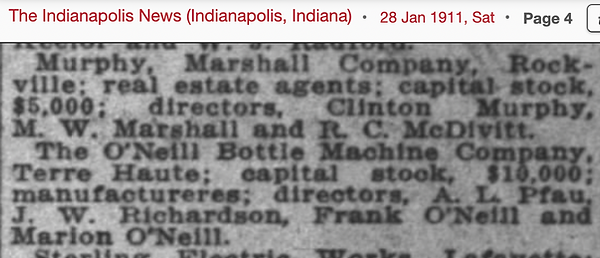

Article about working in a glass house - has good photo of a semi-automatic machine being used: https://www.scotlandsglass.co.uk/cms/index.php?option=com_content&task=view&id=91&Itemid=45

You can see here the man adding the metal (liquid glass) to the parison mould. The mould would open with the finish still in the finish mould, the parison would invert, then the bottle mould would close around it and the bottle would be blown.